Introduction to
Heat Cut Plastic Bags
Heat Cut Plastic Bags are plastic bags made by heat cutting process and are widely used in various packaging and transportation fields. They are widely used because of their high efficiency, durability and cost-effectiveness. This article will introduce the manufacturing process, current usage and future development trend of heat cut plastic bags in detail, aiming to provide readers with comprehensive information.
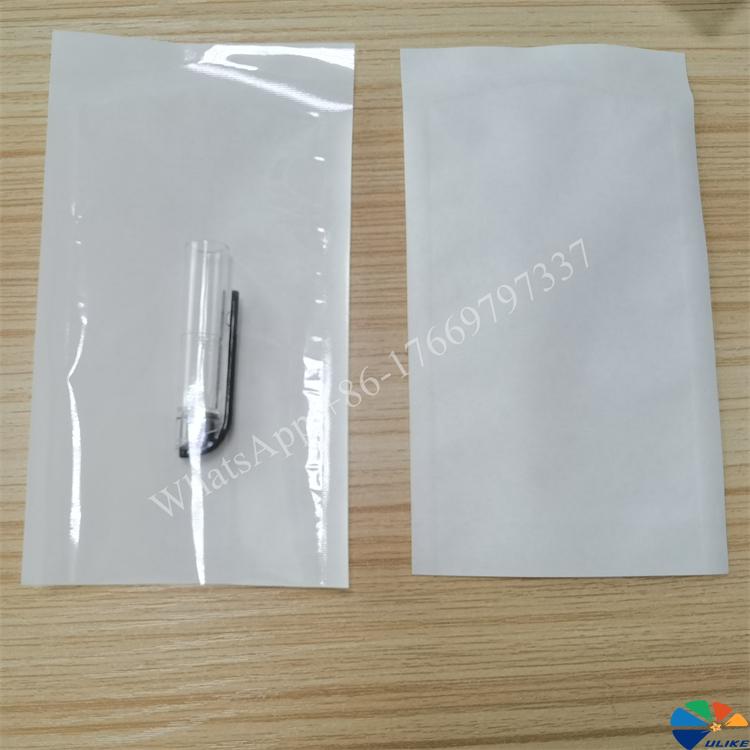
1. Manufacturing process of heat cut plastic bags
The manufacturing process of heat cut plastic bags involves the following steps:
Raw material selection: High-density polyethylene (HDPE) and low-density polyethylene (LDPE) are mainly used as raw materials.
Film blowing process: The polyethylene raw material is melted and blown into film by a film blowing machine.
Printing process: According to customer needs, flexographic or gravure printing technology is used for printing on the film.
Heat cutting process: The printed film is cut into the required size using heat cutting equipment, and the bag mouth is closed by heat sealing technology to form a bag.
2. Current usage status
Hot-cut plastic bags are widely used around the world, mainly in the following areas:
Retail industry: In supermarkets, convenience stores and shopping malls, hot-cut plastic bags are used to package and transport various commodities, such as food, clothing and daily necessities.
Food packaging: Due to its excellent moisture-proof and fresh-keeping properties, hot-cut plastic bags are widely used in food packaging, such as fruits, vegetables and bread.
Industrial packaging: In the industrial field, hot-cut plastic bags are used to package parts, tools and raw materials, which play a role in dustproof, moisture-proof and pollution-proof.
Medical field: In the medical industry, hot-cut plastic bags are used to package medical devices, medicines and disposables to ensure their safety and hygiene.
3. Future development trend
Application of environmentally friendly materials: With the improvement of environmental awareness, hot-cut plastic bags will use more degradable and renewable materials, such as PLA (polylactic acid) and PHA (polyhydroxyalkanoate) to reduce the impact on the environment.
Smart packaging technology: In the future, smart packaging technology will be used in hot-cut plastic bags, such as embedding RFID chips to achieve product tracking and management and improve logistics efficiency.
Multifunctional design: Heat cut plastic bags will develop in a multifunctional direction, such as adding self-sealing strips, anti-counterfeiting labels and anti-theft devices to meet the needs of different customers.
Lightweight and high strength: Through the advancement of material science and manufacturing processes, heat cut plastic bags will become lighter and thinner while maintaining high strength and durability, reducing material usage and costs.
Circular economy model: In the future, the recycling and reuse of heat cut plastic bags will become an industry trend, promoting the closed-loop circulation of plastic bags, reducing resource waste and environmental pollution.
Conclusion
Heat cut plastic bags are widely used in various industries for their high efficiency, durability and cost-effectiveness. With the advancement of technology and the improvement of environmental awareness, heat cut plastic bags will develop in the direction of environmentally friendly material application, intelligent packaging technology, multifunctional design, lightweight and high strength, and circular economy model. These trends will not only help improve product performance and user experience, but also promote the sustainable development of the industry.